
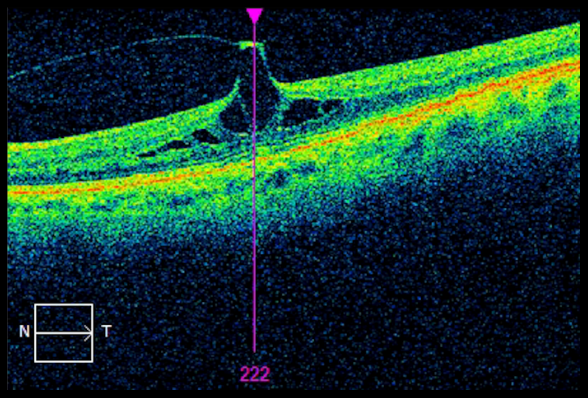
They provide the machine driver with additional information and control parameters during tunnel advance.įor example, software solutions for segmental lining calculate the optimal ring sequence and monitor ring deformation. To increase safety during tunnelling and improve the quality of the tunnel structure, VMT develops complementary systems for monitoring and automating process sequences. Monitoring for segmental lining and pipe jacking The expert system TUnIS Navigation MT LaserTotalstation, used for drives from DN1600 upward and requiring 50% fewer control measurements than the gyro system due to its high level of accuracy. The gyro-based all-rounder system TUnIS Navigation MT Gyro, requiring no line of sight between the components and particularly well suited for drives with small diameters and tight curve radii. For these the platform offers two options: Long-distance and curve drives can be navigated just as precisely with TUnIS Navigation MT. Depending on the project configuration, this makes it possible to navigate straight drives up to 450 m long (TUnIS Navigation MTHydroLevel). In order to neutralize refractory effects acting on the laser with increasing tunnel length, the base system for calculating the vertical machine position is supplemented with an electronic hose water level. An integrated inclinometer measures pitch and roll (TUnIS Navigation MT Laser). This enables horizontal and vertical deviations from the nominal values to be identified. For short, straight tunnelling sections of up to 250 meters, a tunnelling laser is installed in the launch shaft, whose reference beam hits a target in the rear of the TBM. In pipe jacking in particular, tunnelers stay on track with the modular navigation platform TUnIS Navigation MT developed by VMT. Often geology and topography demand curve drives, or differences in height have to be overcome. For non-accessible tunnels and projects in the smaller diameter range, due to the limited space available in the machine the control container is decoupled from the TBM via a bus system and placed at the launch shaft.Įven in the case of pipe jacking alignments, straight tunnel routes tend to be rare. In the event of exceeded tolerances, warnings appear to prevent settlement and heaving and the TBM driver can intervene. Computer-aided applications compare the measured values with the targets. Sensors and measuring devices record relevant tunnelling parameters, such as speed, the torque of the drive, the contact pressure of the cutting wheel or the support pressure in the excavation chamber. The equipment used depends heavily on the customer's requirements. From here he operates the steering cylinders and maneuvers the machine with absolute precision and control along the planned tunnel axis through the underground, even on the most difficult alignments and in the most challenging geologies. With state-of-the-art process and control technology, the TBM driver in the control cabin keeps track of the situation while tunnelling is in progess. They determine the exact position and movement tendency of the machine and display it to all relevant project participants in real time. For this reason all Herrenknecht projects use reliable navigation systems from our subsidiary VMT. Controlling and navigating a TBM requires the utmost precision along the entire route until the final breakthrough.
